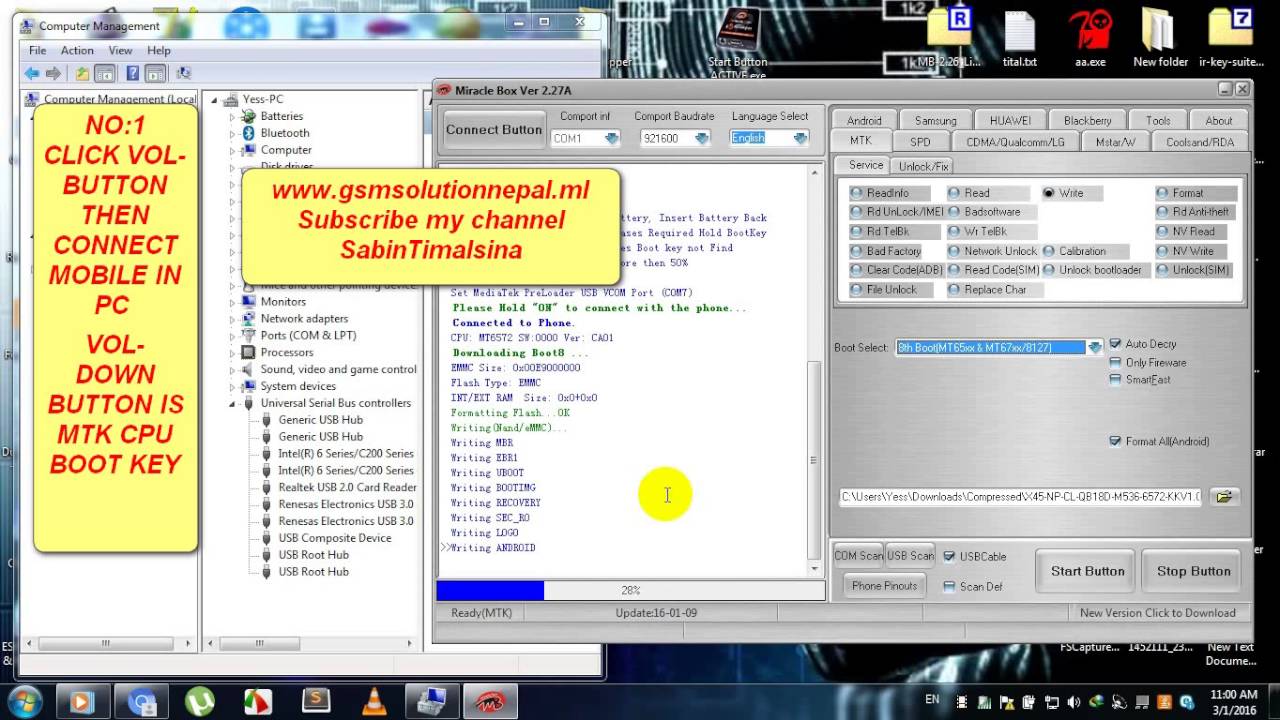
Download File Firmware and Flashtool plus Video Tutorial compressed:
do not forget there are some additional tips from me:
How To Flashing colors x45
this video will show you how to coatyour ar-15 lower receiver or other gun parts with brownells aluma-hyde ii aerosol. here are the tools and materials you will need. your lower receiver or other gun parts that have been cleaned and dried. a quarter inch bolt to install into thelower receiver's pistol grip hole. it should be 28 thread pitch and aboutfour inches long to provide a good handle for turning the lower receiver. brownells tce cleaner/degreaser which will remove any remaining oils from the part before spraying. brownells aluma-hyde ii in whatever color you have chosen.
disposable gloves to keep your non-spraying hand from getting coated with aluma-hyde ii. optionally you can use a heat gun or hairdryer to speed up the time between coats. if you intend to oven cure you will need an oven preheated to 300 degrees fahrenheit. put one rack to the top position and remove all others if you plan to hang the parts. test the fit of your parts prior toheating the oven and starting work. you will also need a way to hang the part in the oven and i'm using a binder clip for that purpose. i'll also use a piece of aluminum foil as aheat shield in the oven between the parts and the heating element. the first thing we will do is figure outa way to hold and turn the part without
touching the surfaces that will becoated. in the case of this ar-15 lowerreceiver the quarter inch bolt will do the trick. the next step is to make sure everythingis ready before we start. this means preheating the oven, plugging in the heat gun or hair dryer, making sure the can of aluma-hyde ii isthoroughly shaken up and that both the tce and aluma-hyde ii cans have their tops removed. note: if it is cold outside keep all of yourparts and aerosol products inside until you are ready to spray so theystay warm and then bring them back inside to rewarm between coats.
now go outside in a well-ventilated area and spray the part was tce. the tce is very volatile and will flash off fairly quickly but you can speedthe process by use of a heat gun. here you can see a makeshift holder forthis circular part that is just some pieces of masking tape used as a handle. onceyou are sure the part is dry and free of tce you can spray the first coat of aluma-hyde ii. even though i shook the can up the first spray that came out was clear liquidand not the matte black. this is why it is a good idea to testspray away from your part. it's also a good idea to purchase extrafan pattern spray nozzles from brownells
as these can become clogged which didhappen while i was spraying this receiver. the part number is 084-179-005. keep the spray nozzle about afoot from the receiver when spraying. start with the tougher areas to reach suchas the fire control group pocket, receiver threading, under receivertrigger area and the front of the receiver. the sides of the receiver are the easiestto coat so save them for last. do not spray too heavily as we will bemaking four light coats in total. after the initial coat allow thereceiver a few minutes to flash off. you can use the heat gun or hair dryer to gently warm
the surfaces to help speed the process but don't go too hot or too close to thereceiver. after the surface has flashed repeat the process again for a secondlight coat. start with the same nooks and cranniesbefore finishing with the two sides. i have found aluma-hyde ii is fairly forgiving when it comes to runs so don't try to wipe receiver if you getone. just let it dry slowly without heat and it should fade away. subsequent coats will help cover any minor variations. repeat the process a third and fourthtime as needed.
the final coats will be giving thesurface it's finished look and you may not even need to spray the unseen areas such as the magwell and fire control group pocket. focus on asmooth spray for the final coat as the receivershould already be fully covered by now. allow the final coat to flash naturallywithout the use of a heat gun or hair dryer. pull the nozzle from the spray can andsoak it in some acetone to clean it out. otherwise it can clog up. finally we are ready to bake the receiver for one hour at 300 degrees fahrenheit. fair warning, this will smell up thehouse for a few hours.
not terrible but it won't smell like freshbaked cookies either. being very careful not to let thereceiver touch anything, especially in the oven, clip the quarterinch bolt to the top rack. make very sure the clip is secure so thereceiver doesn't fall. i also use a piece of aluminum foil to act as a heat shield between the heating element and the receiver. i want the receiver to cure from theheat of the oven not from the more direct and extreme heat of the element. for the small circular part i haveimprovised a piece of aluminum
foil as a twist tie. gently close the ovendoor and set the timer for one hour. after the hour is up shut the oven off butleave the parts in the oven for another hour so the heat comes down gently. after that hour is up i carefully openthe oven door and allow it to sit another half hour with the door open before removing the parts. that's it. here you can see some spottingin the coating of this cast aluminum receiver due to the clogged nozzle but the surface itself is flat. after curing i spray the receiver with oilwhich will darken and lubricate it. wipe off the excess with paper towelsand you're ready for assembly with your parts kit.
thanks for watching and be sure to visit the 80percents.com web site for more tips, reviews of 80% lower brands and to joinour 80% lower builder forum.
0 comments:
Post a Comment